Tension in Welds
What is it?
After welding, shrinkage during cooling can cause high tensile stresses in the weldment. These high tensile stresses leave the welds in tension.
In a Lambda Technologies study on austenitic alloy weldments type 304L and 316L stainless steel and Ni-based alloys weldments including Alloy 22, welding produces high tensile residual stresses of greater than +100 ksi (+689 MPa) at the surface and into the near-surface material.
Why does tension in welds cause failure in critical components?
Welds in tension are vulnerable to stress corrosion cracking (SCC). SCC results when a susceptible material is exposed to a corrosive environment with tensile stress above a certain threshold. SCC can lead to component failure.
Material degradation problems due to SCC in the U.S. nuclear industry alone have cost more than 10 billion dollars in the last 30 years.1
How can you mitigate tension in welds?
If you introduce a designed compression into the surface after welding, this mitigates tension and eliminates the possibility of crack propagation from SCC. Low plasticity burnishing (LPB®), is applying a designed compression that provides greater depth of compression than conventional shot peening. This leaves a smooth surface finish and protects the surface against SCC with the added benefit of low cold working for thermally stable residual compression.
Learn more about Low Plasticity Burnishing from Lambda Technologies Group and how it can prevent tension in welds in your critical components.
1“Primary system Corrosion Research.” EPRI Portfolio, 2008. EPRI Website 11/12/07 http://portfolio.epri.com/project.aspx.
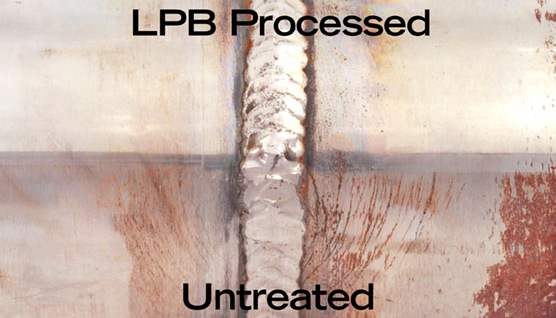