LASER SHOCK PEENING
*Welcoming clients from our friends at LSP Technologies in Dublin.*
Laser peening, also referred to as laser shocking or laser shock peening, is a high-energy, short laser pulse that impacts a metal surface creating indentations and regions of residual compression.<
Common Issues with Laser Peening
Cost, quality control, and logistics are all limitations of laser peening.
- Laser peening equipment requires a high capital cost, which may include a clean room environment and million-dollar-plus installations.
- Laser peening requires a component to be repeatedly coated with tape to produce the depth and magnitude of compression needed. Two coating cycles are usually required to achieve the desired depth of compression.
- It is difficult to control the processing variables. Variation in thickness and turbulence of the water layer tamp, and the debris in the air and on the mirrors can affect compression, even with precise control of the laser.
Internal cracking caused by the superposition of the shock waves from opposing faces of blades or echoing waves from the opposite wall of thicker sections has been found to limit the application.
Review our case study on LPB vs Laser Peening: R0
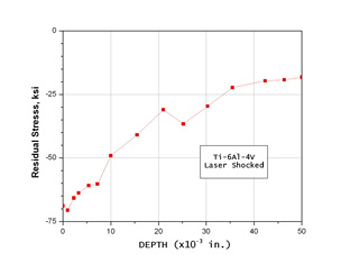
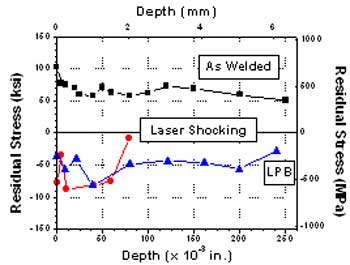
LPB Provided Much Deeper Compression
Alternate Processes Offered by Lambda Technologies Group
Low Plasticity Burnishing (LPB®) >
also introduces deep, beneficial compressive residual stress into materials with minimal cold work. It is significantly less expensive than laser peening, requires a single application, and is easily implemented in existing manufacturing or maintenance environments.
Controlled Plasticity Burnishing (CPB™) >
is a variation on our award-winning LPB treatment, specifically designed for applications where low cold work isn’t necessary.
Controlled Impact Burnishing (CIB™) >
is designed for seemingly unreachable geometries, treating vulnerable areas of a component with highly controlled impacts to impart a deep, stable layer of beneficial compressive residual stress.