Finite Element Analysis & Modal Analysis (FEA/FEM)
What is Finite Element Analysis?
Finite Element Analysis (FEA) is numerical modeling of a component or system to predict behavior under a given condition.
FEA uses the finite element method (FEM) to model the response of an object to various inputs mathematically. FEM is the dominant discretization method in structural mechanics, whereby a structure is broken down into pieces or elements. Elements are connected via nodes, which results in a set of simultaneous equations that can be used to understand how a system reacts to mechanical and thermal loads and specific boundary conditions.
How is FEA used at Lambda?
Lambda Technologies provides finite element analysis (FEA) services in support of residual stress design and characterization. Residual stresses can be designed to increase the fatigue performance and damage tolerance dramatically and mitigate stress corrosion cracking (SCC) for critical components used in all essential industries. Lambda uses several commercial FEA software packages as well as specialized macros and subroutines written by Lambda engineers specifically for residual stress analysis and design.
Features of Lambda’s
Finite Element Analysis Services:
- Design of compressive residual stresses using Lambda’s patented Fatigue Design Diagram (FDD) to meet specific component performance goals
- Determination of distortion and compensating tension produced by surface treatments
- Determination of in-service applied stresses
- Analysis of modal shapes, natural frequencies, and associated vibratory stresses
Applications:
- Optimization of compressive residual stress
- Rigorous layer removal correction of arbitrary geometries in support of subsurface x-ray diffraction residual stress measurement
- Optimization of machining sequence to minimize distortion
What is Modal Analysis?
Modal analysis determines the vibration response of a structure. The natural or resonant frequencies of a component can be determined both empirically and theoretically using modal analysis. A part’s natural frequencies can be used to understand the range of operational frequencies a part can operate.
How is Modal Analysis used at Lambda?
Lambda offers modal analysis services for determining the natural frequencies of components. Component distortion, or part-to-part variations in geometry, can result in differences in the natural frequency. An unexpected shift in the natural frequency of a critical component may increase the operational stresses depending upon the loading spectrum.
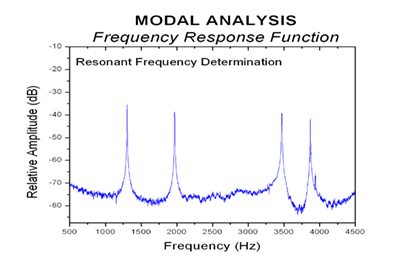
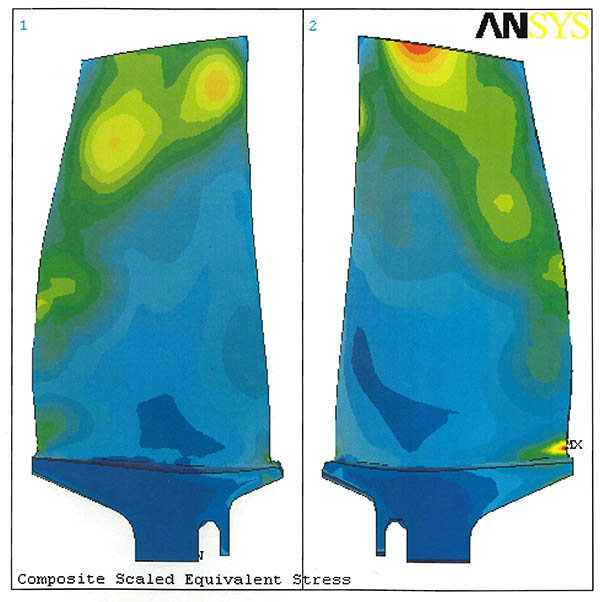
Features of Lambda’s
Modal Analysis Services:
- Accurate assessment of modal frequencies with frequency response functions (FRF)
- Data reduced from time domain to the frequency domain using Fast Fourier Transforms (FFT)
- In-house procedure for statistical analysis and presentation of frequency shift between individual samples or groups of samples
- Finite element determination of vibrational response
Questions about our testing parameters or techniques?