Quantitative Phase Analysis
What is X-Ray Diffraction Quantitative Phase Analysis?
Quantitative phase analysis is the measure of relative proportion of elemental constituents or phases using X-ray diffraction (XRD) patterns. The intensities of the diffraction lines of a particular phase of a mixture depends on the relative amount of that phase in the mixture.
Quantitative phase analysis can be used to measure not only types of compounds but also the amount present in a solid or powder system. Diffraction analysis has advantages over ordinary chemical analysis; the diffraction method will reveal the presence of compounds whereas chemical analysis can only provide elemental information. Quantitative phase analysis can be used for plasma spray process development and quality control testing of coatings. Quantitative analysis can be used to determine trace silica in ceramics and minerals, and provide quality control of austenite content in heat-treated steel components.
How is it measured?
Lambda’s quantitative phase analysis is based upon the rigorous Reference Intensity Ratio (RIR) method. Procedures developed for specific systems of phases are “calibrated” by either calculation of the material dependent on structure factor portion of the RIR, or by direct measurement using mixtures of known powder components. All procedures developed at Lambda are tested using known mixtures before application. Systems of ceramic, alloy, or mineral components may be analyzed in either solid or powdered form. Complete facilities for sample preparation, sectioning, polishing, pulverizing, and sizing are available.
Lambda has developed unique quantification software allowing complex diffraction patterns to be analyzed. A variety of algorithms are available for background subtraction, diffraction peak integration, and peak profile deconvolution in any combination. Once technique files controlling the software have been developed for a system of phases, the diffraction data analysis for subsequent samples is independent of any subjectivity on the part of the technician.
Lambda employs three methodologies in quantitative analysis determination:
Methodologies
1. Internal Standard
The Internal Standard Method is the procedure of choice for analyzing powdered systems. A known quantity of a reference powder is added to an amount of the test specimen. Any number of constituents in a mixture may be quantified independently. The mixture may contain amorphous (noncrystalline) components and the mass absorption coefficient of the mixture need not be known in advance. The Internal Standard Method is applied broadly to any mineral or materials systems for which the chemistry is unknown.
2. External Standard
The External Standard Method may be applied to solid systems, such as alloys, plasma sprayed coatings, or oxide layers. This method allows the quantification of one or more components in a system that may contain an amorphous fraction. The mass absorption coefficient must, however, be known in advance, requiring either full elemental chemistry or prior knowledge of the chemistry, as in the case of plasma spray coatings or alloys.
3. Direct Comparison
This procedure requires no standards but is only applicable to full crystalline mixtures. All of the components in the system must be quantified for solution. The Direct Comparison Method is the common method used for retained austenite determination
Features:
- Graphite monochromators provide virtual immunity to fluorescence from the sample for optimum detection limits and precision.
- All diffractometers at Lambda are calibrated to the NIST mica and silicon standards (SRM 675 and 640) and corrected for angular error using algorithms unique to Lambda Research’s data collection software.
- The data collection and reduction software developed at Lambda can be tailored for specific applications allowing detection of extremely broad peaks and deconvolution of overlapping peaks.
- Rapid, non-destructive analysis using the External Standard Technique.
- Percent crystallinity from the sum of the crystalline components.
- RIR determination for technique development.
- Reproducibility of data collection and analysis, and elimination of subjectivity.
- Speed, accuracy, and reduced cost to support effective quality control testing.
Application Examples:
- Plasma-sprayed hydroxylapatite coatings and powders
- Volume percent retained austenite determination
- Trace crystalline silica analysis.
- Ceramics and alloys.
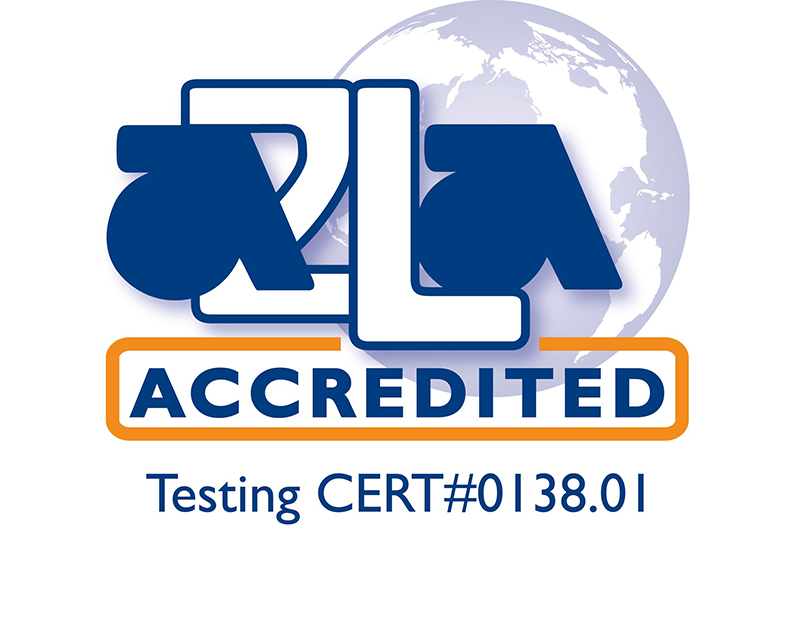
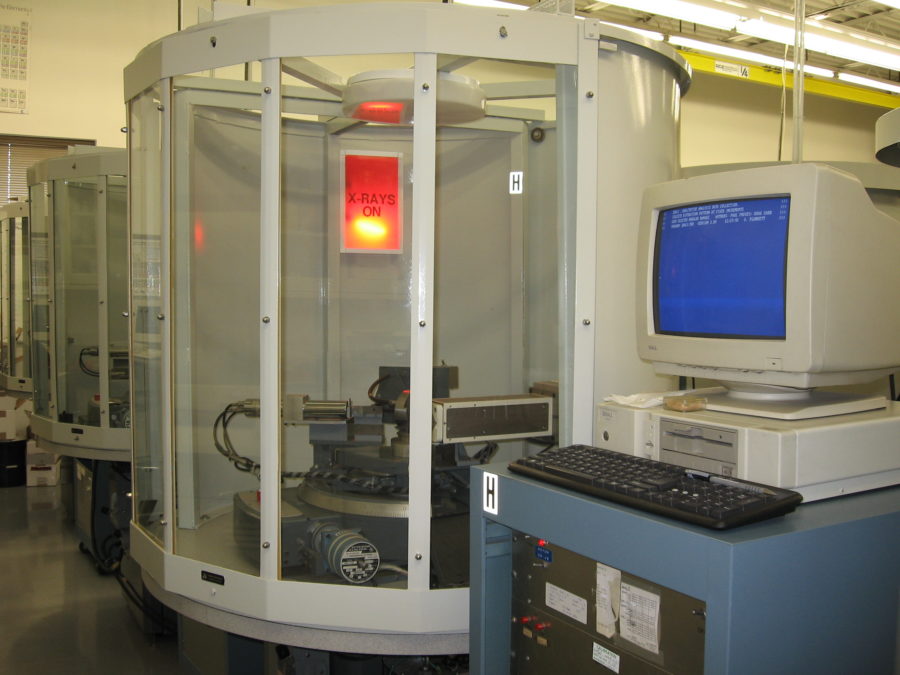
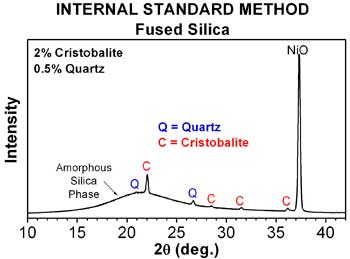
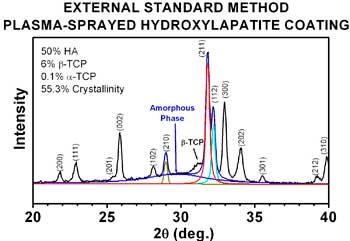
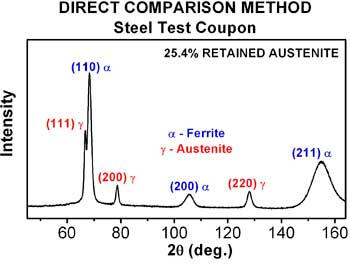
How are Lambda’s services superior?
Our custom-built diffractometers are specifically designed for phase analysis to guarantee accurate results. Diffractometers are calibrated to NIST standards, and all testing is done to ASTM and SAE standards where applicable. Lambda’s experience in data collection, phase identification, and analysis provides the ultimate data quality and support to our customers.
Questions about our testing parameters or techniques?